Production for Better Shelter has begun
Production for Better Shelter has begun
On August 31, 2021, we officially launched the production of plastic insulation panels into a modular housing system that serves as accommodation for families displaced by war conflicts, persecution or natural disasters. SPUR will thus become the sole supplier of roof and side panels for Better Shelter, supported for its global benefit by the IKEA Foundation. For this purpose, a new production hall was created in the existing premises and new technologies were installed, including a robotic press room.
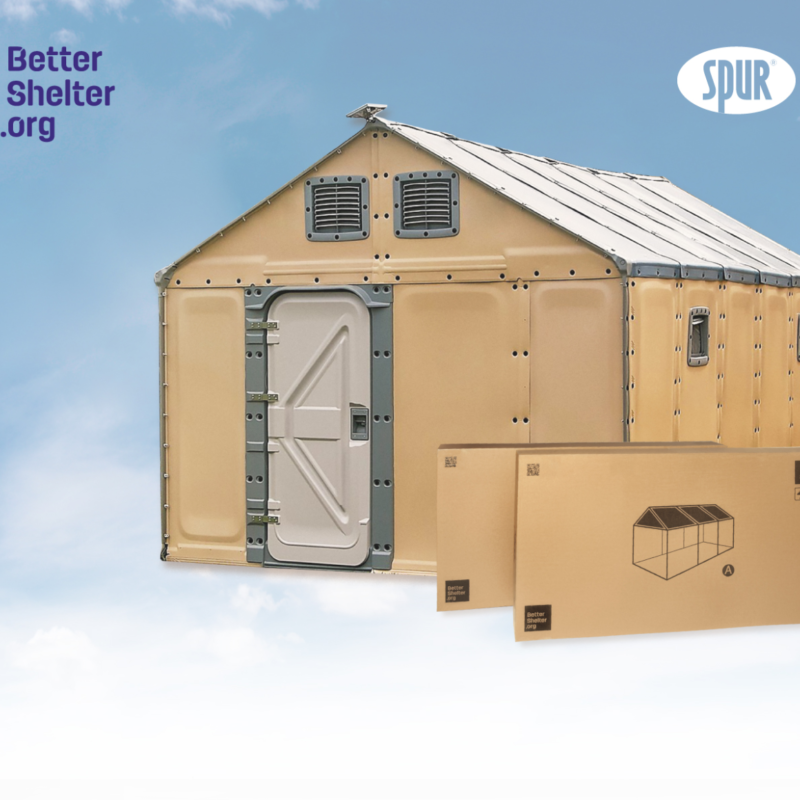
“This is an efficient, fast and cost-effective temporary accommodation solution designed to meet the needs of providing basic housing, privacy and security for people affected by adverse circumstances,” said SPUR’s CEO Tomáš Dudák, adding that the company was working on preparing the production and material development for three years. It must meet demanding requirements for non-flammability, thermal insulation, resistance to wind and rain, protection against UV radiation and health safety, and it must also be light and easy to store for transport and handling.
“These are sheets made of polypropylene foam used, for example, in cars, which are additionally provided with special foils on both sides. Panels constructed in this way achieve unique useful properties while maintaining mechanical resistance, are very light and fully recyclable, as they are a single type of plastic. For this part of the production process, we constructed and put into operation a line for laminating all sandwich layers. The process of joining the materials takes place without the use of adhesives,” explained Tomáš Dudák.
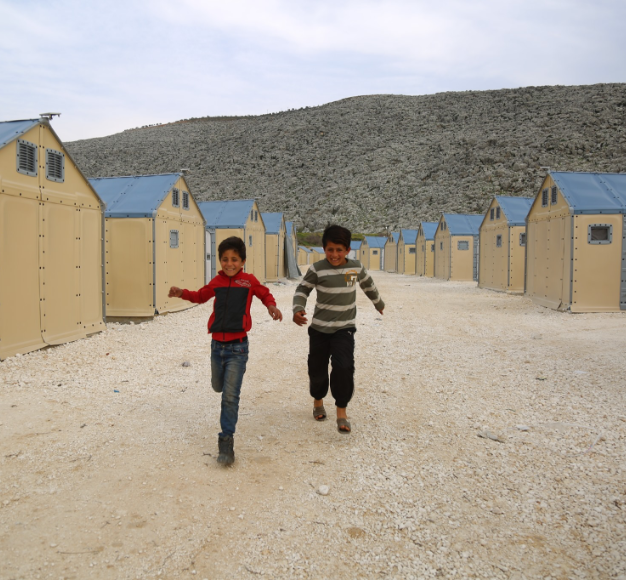
New production hall
The new Better Shelter production hall is equipped with a fully automated robotic press. Part of the production process is also the production of the basic polypropylene lightweight board on the extrusion line and subsequent lamination. The total investment in the project was over 100 million CZK. The capacity of the technology during three-shift operation enables the production of components for 30,000 “houses” per year.
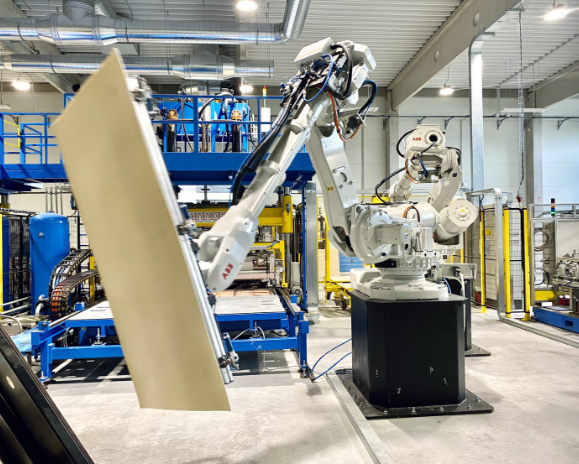
The “house” has an area of approx. 17.5 m2 and provides accommodation for 4 to 6 people. It consists of polypropylene foam sandwich panels, galvanized steel structure, plastic fasteners and other accessories such as door lock, solar panel, LED lamp or insect protection nets. It is transported to humanitarian aid areas in an unfolded state in two cardboard boxes with a total weight of approx. 160 kg. A team of 4 people can build it in 5 hours. “The guaranteed service life of the panels is at least 3 years in the most demanding climatic conditions anywhere in the world, for example on the equator. However, the actual usability of a temporary residence is an average of 7 years, which is unfortunately also the time that refugees in some parts of the world spend in these camps,” added Tomáš Dudák.
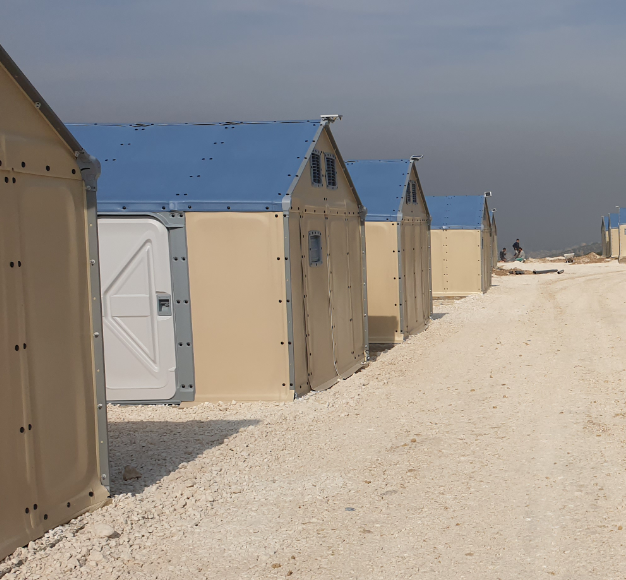